Looking as far back as the World War II era, history has proven the military implications of manufacturing. The U.S. Department of Defense (DOD) is one of the largest industrial customers in the world, and both the U.S. economy and national security rely on maintaining a world-class manufacturing sector and a constant culture of innovation.
When people hear the term “manufacturing,” many envision a factory where raw material is transformed into a product through manual or automated operations. Advanced manufacturing, however, refers to a field of research and technology encompassing all aspects of manufacturing, from preproduction to postproduction. It incorporates basic research, such as physics or biology, and applied research, such as mechanical engineering or microbiology.
Ultimately, this work helps the manufacturing industry adopt new technologies to reduce life-cycle energy and greenhouse gas emissions, reduce stock material waste, lower production costs and create new products for the aerospace, automotive and defense industries, among others.
Modernizing the Military
Tony Schmitz, a professor in UT Knoxville’s Department of Mechanical Aerospace and Biomedical Engineering with a joint appointment at Oak Ridge National Laboratory, says the everyday challenges that arise when the manufacturing industry faces obstacles are clear.
“For example, the global impact of the COVID-19 pandemic on manufacturing has caused supply shortages in both goods and services around the world,” he says.
Maintaining the U.S.’s technological superiority in advanced manufacturing is one issue that unites policymakers from across the political spectrum. Presidents from the past three administrations have issued executive orders referencing the country’s critical reliance on advanced manufacturing, Schmitz says.
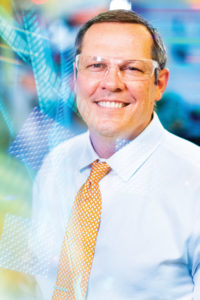
A strong manufacturing sector ensures the U.S. maintains a ready supply of the goods and services needed for economic growth and national security and assures the integrity of mission-critical items for the military.
In 2021, the U.S. government turned to UT Knoxville to help it stay ahead.
A $22.5 million grant from the DOD will allow UT Knoxville researchers to focus on improving materials and manufacturing methods to significantly advance the Army’s top two modernization priorities, next-generation combat vehicles and long-range precision fires. U.S. Sen. Marsha Blackburn, R-Tenn., co-sponsored this work and continues to support UT’s efforts in advanced materials and manufacturing research. This award is part of a five-year, $50 million collaboration among UT Knoxville, the University of Kentucky and the Army Research Laboratory seeking solutions to tackle the Army’s critical modernization challenges through research and development.
The project’s public impact will enhance military capabilities and focus on research and workforce development solutions for the aerospace, automotive manufacturing and energy production industries. UT Knoxville’s contribution will draw on expertise across colleges and departments and include multiple projects focused on hybrid manufacturing, advanced metrology and new techniques for materials processing.
“The research addresses three distinct materials types: metal alloys, polymers and ceramics,” says Bruce LaMattina, senior director for space and defense programs and research professor at UT Knoxville. “The goal is to optimize performance for today’s applications while also overcoming material limitations that will open the design landscape for yet unimagined ones.”
Advanced manufacturing techniques use novel ways of placing different materials within a structure to create new hybrid materials—ideas previously only possible within computer models.
“To accomplish this decades-old dream, there are no less than 14 faculty members from four different departments contributing to the research,” LaMattina says.
Suresh Babu, UT Knoxville–ORNL Governor’s Chair for Advanced Manufacturing, and Schmitz, along with their students, are leading research in hybrid manufacturing at the UT Machine Tool Research Center using a state-of-the-art MELD Manufacturing machine.
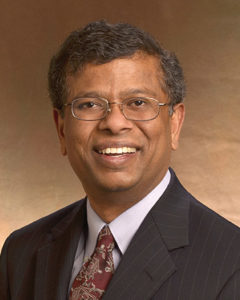
MELD Manufacturing is a woman-owned manufacturing company that has launched a new low-cost and environmentally friendly technique for solid-state additive manufacturing, a type of 3D printing for metals.
“3D printing, or additive manufacturing, is best known for the low-cost desktop printers that fuse layers of plastic filament using a heated nozzle to produce parts, a bit like a hot glue gun,” Schmitz explains. “But it’s also possible to 3D print metals, where metal wire or powder replaces the plastic filament, and an electric arc, laser or electron beam is used to melt the wire or powder layer by layer.”
The MELD machine brings a new approach to that by using a process called friction-stir additive manufacturing.
“This process is known as solid-state manufacturing because the metal is a solid rod, and no melting occurs,” Schmitz says. “Instead, the rod is rotated in a spindle and pressed against the previous layer to give frictional heating, like rubbing your hands together. This frictional heat is sufficient to soften the metal and cause it to deform into the next layer without melting.”
Not melting means the metal does not go through phase changes that can cause voids to form or other issues weakening the product. In practical terms, using MELD technology may offer a cost-effective alternative to significantly decrease the time it takes to produce metal items, such as forgings, needed to build or repair critical items such as ground combat vehicles.
UT’s Academic Advantage
UT Knoxville is now one of only six universities in the nation with MELD machines and the only one in the Southeast. For researchers such as Babu and Schmitz, having this state-of-the-art machine tool on campus is both exciting and noteworthy, as the friction-stir process for 3D printing metal parts is an emerging technology with the potential to revolutionize additive manufacturing capabilities.
“The MELD process has roots to friction stir welding technology that was developed in the 1990s by the Welding Institute; the innovations in MELD are related to the ability to mix many materials to arrive at site-specific properties,” Babu says. “In this work (for the Army), we are leveraging fundamental materials science theories and modeling to arrive at new structures that can respond to different environmental conditions.”
Schmitz and his students are combining MELD technology with other processes available at UT Knoxville’s Machine Tool Research Center to create a conglomeration of processes and combinations to complete their portion of the Army project.
“By combining the MELD additive manufacturing capability with a 3D measuring system and computer-numerically controlled—CNC—machining, we are developing a hybrid manufacturing system that will address Army and U.S. industry needs for large-scale precision part production,” Schmitz says.
Partners in Progress
Advanced manufacturing research is uniquely conducted in partnership among academia, industry and government so new products and processes can quickly move from laboratories and classrooms into the workforce and ultimately into the hands of consumers.
Faculty and students from UT Knoxville’s Tickle College of Engineering are deeply involved in this groundbreaking advanced manufacturing and materials research, working to solve modern challenges while focusing on sustainable practices to improve performance and reduce waste.
“Conventional manufacturing techniques such as extrusion, casting and molds remain critical to U.S. manufacturing, but with technologies such as 3D printing, we have new capabilities to produce geometries that were previously not possible,” explains Joshua Kincaid, a Ph.D. student in the Department of Mechanical and Biomedical Engineering at UT Knoxville. “We can also add strength while using less material. This leads to reduced waste and energy use. The applications for 3D printing continue to expand.”
During the past decade, UT Knoxville has risen as a leader in advanced manufacturing and materials research, particularly within the Southeast region of the U.S. In addition to the multiple laboratories and centers on UT Knoxville’s campus dedicated to this research, faculty and students benefit from several valuable corporate and government partnerships maintained by UT’s Tickle College of Engineering with agencies and corporations, including Oak Ridge National Laboratory, Y-12 National Security Complex, IACMI–The Composites Institute, Lockheed Martin, BAE Systems, Eastman and Siemens, among many others.