Featured photo: Ken Brown, UTHSC executive vice chancellor and chief operations officer, left, and Harry Kochat, Plough Center director
By Peggy Reisser
Photos by Lisa Buser
When a series of flatbed trucks pulled up to a building on the eastern edge of the UT Health Science Center’s campus on a winter morning in 2016, it was impossible to imagine the enormous steel structures they carried would one day house a manufacturing operation that could help save lives.
The trucks were delivering three prefabricated structures similar to large shipping crates or trailers, so big they had to be loaded by crane into the building through an opening in the sidewall. Made by G-CON Manufacturing in College Station, Texas, these structures, called PODs, would eventually become sterile or cleanroom space for the manufacture of pharmaceuticals.
Today, each of those 800-square-foot PODs are well-integrated as cleanrooms and form the guts of UTHSC’s newest entrepreneurial venture, the Plough Center for Sterile Drug Delivery Solutions, a state-of-the-art, contract pharmaceutical manufacturing facility.
The new Plough Center, located at 208 South Dudley Street near downtown Memphis, is the only pharmaceutical facility of its kind in Tennessee and one of the few university-owned contract manufacturing facilities in the United States. It is expected to raise the university’s standing in the national and global marketplace and position the university to help speed the process of bringing new drugs to market.
Now in the final stages of qualifying equipment, personnel and processes before manufacturing of pharmaceutical products begins, the center has three clients, all Tennessee companies, waiting in the wings with drugs ready to produce. The $20 million facility, which once housed a discount clothing store and a print shop, now encompasses 20,000 square feet, including the cleanrooms, support labs, offices and training facilities. There is room for expansion as business grows.
The Plough Center will produce small-batch drugs in injectable and freeze-dried forms for preclinical, Phase 1 through Phase 3 human clinical trials; over-the-counter medications; prescription commercial batches; generic drugs to meet drug shortages at affordable prices; orphan drugs developed to treat specific and rare diseases; and innovative drug delivery systems to meet various unmet clinical needs. It has the capacity to produce 15,000 to 20,000 filled vials or syringes per day in multiple shifts for clients, including start-up companies, virtual companies, small pharmaceutical developers, researchers and even makers of veterinary medicines.
Operations, including the lines for filling, capping and labeling, are fully automatic with minimal operator exposure to the drug products manufactured. This nearly zero exposure of operator to product eliminates human intervention and mediates drug product recalls and batch failures due to cross-contamination.
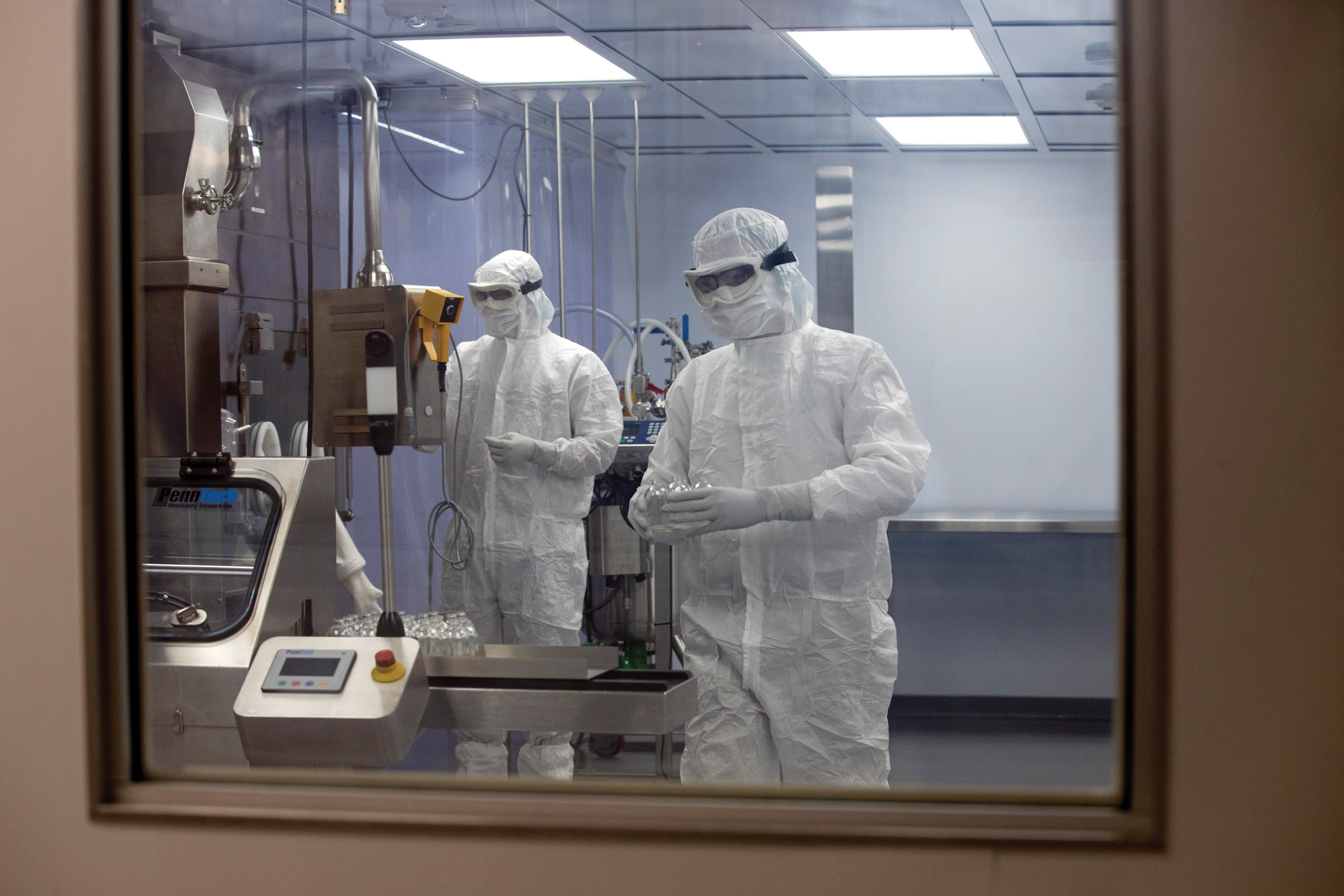
Think of a sterile lab from any space movie, and you’ll get the picture. Specially trained staff wearing personal protective equipment must move through airlocks to enter the production space, only after it has undergone multiple standardized sanitization protocols to maintain the sterile environment. Constant attention to maintaining this sterile environment is essential.
“We are in the final stage of doing potential client-based performance qualifications of all equipment, personnel and manufacturing steps,” Harry Kochat, Plough Center director, says. “Once this is successfully done, we register this facility with the FDA (Food and Drug Administration).”
At that point, production can commence.
The Plough Foundation gave $4.5 million in seed money to support the new facility. Ken Brown, UTHSC executive vice chancellor and chief operations officer, has led the development of the new facility and serves as its executive director.
“We’re very excited about this particular project,” Brown says.
The new facility expands the capacity of the university’s smaller, existing Plough Center in the Van Vleet Building at 3 North Dunlap Street across campus. Originally called the Parenteral Medication Laboratories, it has a half-century legacy in manufacturing drug products and offering training in sterile product preparation for clients on a much smaller scale. In fact, Kochat says the first batch of an oncology drug he developed in the 1990s while working in Texas was produced at that facility and used at St. Jude Children’s Research Hospital to treat brain tumors in children.
The two Plough Center locations together offer about 3,900 square feet of Good Manufacturing Practice (GMP) compliant processing space. GMP protocols ensure that products are consistently produced and controlled according to FDA quality standards for the manufacture of sterile medications.
In addition to the production capabilities, the facility gives UTHSC leadership recognition for training students and professionals from the drug industry and government regulatory agencies in sterile pharmaceutical production techniques and cleanroom behaviors.
It also puts UTHSC in a position to have a local, national and global impact on drug development and delivery, particularly for countries where shortages exist.
“We talk to people in developing countries from the international community, from Kenya in particular, where there are significant drug shortages,” Brown says. “We will work with people in these developing countries to teach them how to build these facilities and how to do pharmaceutical manufacturing and compounding to hopefully mitigate some of the drug shortages. So, theoretically, this project has a much more global reach in its evolution than just what it means for us here locally.”
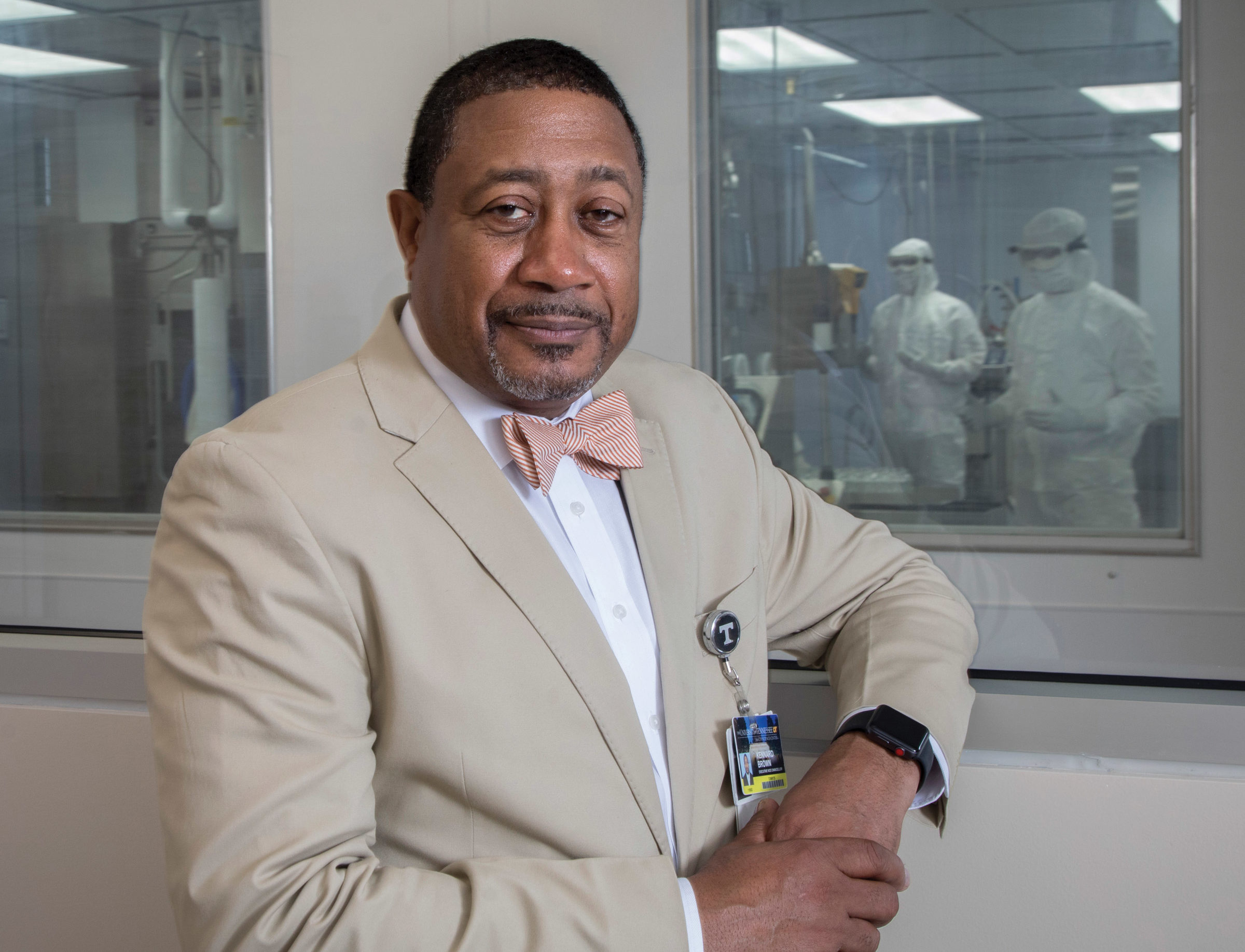
As a member of the Asia-Pacific Economic Cooperation (APEC), Brown has been involved in global pharmaceutical supply-chain safety and security efforts for several years. He has made presentations in China, the Philippines, Peru and elsewhere to senior officials of APEC about the university’s desire to be involved in the global effort surrounding patient safety and product security. He also has hosted delegates from China and Africa at UTHSC to discuss pharmaceutical manufacturing, delivery and safety issues.
“The future is very bright,” Kochat says. “The companies already in line with products are just the beginning.” He says discussions are underway for UTHSC to partner with INDCORE, the Industrial Center of Resources and Enterprising, an international movement headquartered in Puerto Rico, to help spread training in pharmaceutical production and improve access to pharmaceuticals in developing countries.
UTHSC’s new Plough Center for Sterile Drug Delivery Solutions is “a good success story to tell,” he says.